UMB 3D Printer ‘Ear’ To Save The Day
A University of Maryland, Baltimore (UMB) employee’s basement has turned into a small-scale manufacturing operation that is helping front-line health care workers one ear saver at a time.
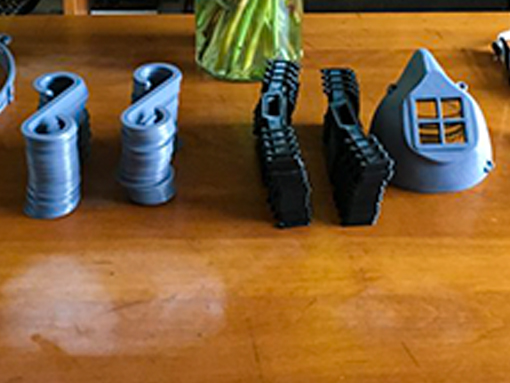
These ear savers and a molded mask are some of the personal protective equipment components that UMB emerging technologies librarian Brian Zelip has 3D-printed from his basement during the pandemic.
Brian Zelip, MSLIS, MA, emerging technologies librarian at the University of Maryland Health Sciences and Human Services Library’s (HS/HSL) Innovation Space, answered the call to arms for 3D printers to help with personal protective equipment (PPE) manufacturing during the COVID-19 outbreak.
“This is Baltimore, where making is a tradition,” Zelip said.
Zelip lugged the 138-pound Raise3D N2 printer from HS/HSL to his Baltimore home during the lockdown as institutions like the National Institutes of Health (NIH) and others released files to print PPE components. His wife’s handbag-making studio is now a miniature PPE plant.
When the University Maryland School of Nursing (UMSON) asked for help from the community with PPE components, Zelip got to work making ear savers for surgical masks. The first batch of 100 was an S-shaped tool.
“They’re wearing these masks for 24 hours a day or more and getting a lot of irritation,” he said. “These things come in handy to help save the day.”
That first order of 100 turned into a request for 500 more. In all, Zelip has printed about 700 parts so far that are delivered to the University of Maryland Medical Center (UMMC) and to the home of Susan Dorsey, PhD ’01, MS ’98, RN, FAAN, professor and chair of the Department of Pain and Translational Symptom Science at UMSON. Everything Dorsey receives goes to University of Maryland Medical System (UMMS) and is parsed out among system staff from there. Out of the thousands of ear savers received at UMSON, Zelip has been the most prolific 3D-printed producer, Dorsey said, with the Archdiocese of Baltimore close behind.
“Not just the volunteers in the community, but for those who are on staff or faculty at UMB, they are doing this work in addition to their regular jobs, which have been much more complicated and difficult in light of this pandemic,” Dorsey said.
UMSON assistant professor Laura Koo, MS, RN, CRNP, FNP-BC, also donated 58 ear savers to UMMC direct patient care workers and about 16 ear savers to co-workers at the UMMC call center, where she is working once a week. She enlisted her 12-year-old daughter and 10-year-old son to monitor the at-home 3D printer. Each ear saver has “COVID-19 Heroes” printed on it.
Zelip has now turned his attention to an adjustable ear saver model made available by the NIH 3D Print Exchange after hearing from University of Maryland School of Medicine (UMSOM) faculty about needs at UMMC.
“It allows for various head sizes with these little tab inserts,” Zelip said.
That adjustable model has provided relief for the nurses who received them, said Paul Thurman, PhD ’18, MS ’07, ACNPC, CCNS, CCRN, a clinical nurse specialist who is coordinating PPE donations at UMMC.
“We have been overwhelmed with the amount of support that’s been coming from Brian as well as others in the community to pull together and make sure everyone is protected while they’re taking care of these patients,” Thurman said.
Nurses will wear their masks all day long other than to eat. Masks with elastic ear loops can cause irritation over the day, Thurman explained.
“Over time, the pressure the elastic places on the ear becomes either painful or some staff have developed breakdown behind their ear because the skin behind the ear is real thin and is right on top of cartilage,” he said. “The device that was 3D printed fits behind the head, and so the pressure is no longer on the ear. It’s distributed over the back of the head.”
About 7,000 employees at UMMC are wearing some type of mask or respiratory protection, Thurman added. Needless to say, the pieces go quick, but can be reused and sanitized. Some pieces have a tendency to break, creating the continued need for more ear savers.
“The plastic piece gets caught on something or they put it on their bag and something is put on top of it and it breaks, and that’s when it needs to be replaced,” Thurman said.
Zelip’s first PPE contributions were headbands and chin pieces for face shields sent to Baltimore makerspace Open Works, where the shields are assembled for health care workers in the area. He printed 28 sets for Open Works that were attached to face shields and sold and distributed to various hospitals.
The high-end, consumer-grade printer works every day on about six hours of sleep. Zelip compared 3D printing to using a hot glue gun, where solid material is inserted that melts and builds layer by layer. Zelip’s model can print layers as small as 0.1 mm tall at a time. Three ear savers take about 90 minutes to print.
Zelip will have to find a way to nurse his printer, as the need for new and replacement ear savers does not appear to be slowing down anytime soon.
“I’m trying to give back to the printer a little bit and coddle it because it’s one of our main hopes right now without doing anything more drastic,” Zelip said.