Student Streamlines Denture Manufacturing
Micah Weisenberg, DDS ’15, is trying to give the denture-making process a breath of fresh air. The fourth-year dental student has developed a patent-pending system that combines air jets with an intra-oral scanner to streamline some steps that are involved in producing dentures.
For many dentists, one of the most challenging steps in denture production is the border molding process, Weisenberg says. During border molding, a dentist uses wet wax to take an impression of a patient’s mouth so that the dentures are fitted properly. But it is difficult to use that wax to take an impression of the narrow area between the upper cheek and the gum. For Weisenberg, the sticky wax made the process slow and uncomfortable for the patient. “I made a mess everywhere,” he recalls. “I was getting very frustrated with border molding, and I started to think, there has to be a better way to do this, for me and my patient.”
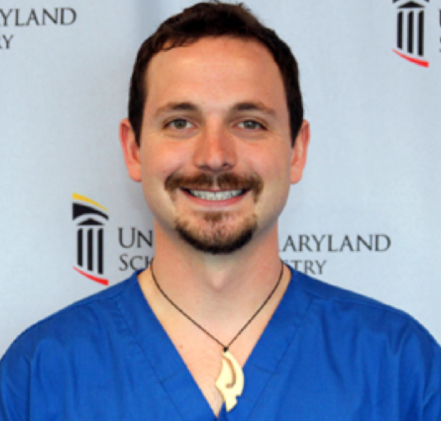
Micah Weisenberg, DDS '15
He decided to see how a new piece of technology, 3D intra-oral scanners, could help improve the process. Dentists use intra-oral scanners to capture video of a patient’s mouth and produce a digital impression with extreme accuracy. These digital scanners are often used to take impressions for dentures, but the devices are unable to effectively scan the narrow area between the upper cheek and gum. Weisenberg found a solution. By fitting a 3D scanning unit with air jets, he was able to pulsate air into that narrow area, moving the gum tissue so he could take an accurate impression using the scanner. The innovation could translate into a less expensive and better fitting and feeling denture.While the device has huge implications for dentures, the air jets also provide better moisture control when scanning for crowns and bridges, compared to current intra-oral scanners, Weisenberg says.
He has developed the idea into two different systems – a 3D scanning unit with built in air jets and a set of air jets that can be retrofitted to an existing scanner. Retrofitting the jets could enable even more dentists to benefit from Weisenberg’s invention, since approximately 10 percent of dentists already use 3D scanners in their practices. This technology, while currently pricey, is only going to become more prevalent in the future, Weisenberg says. “If a dentist is already spending $15,000 to $25,000 for this 3D scanning unit just to do crown and bridge procedures, for a small amount more, they can now use it to produce crowns, bridges and dentures, making the purchase much more justifiable,” he says. “It seemed like a no-brainer to me.”
By avoiding traditional border molding, a dentist could be able to eliminate at least one appointment from the denture-making process, enabling that dentist to provide care for more patients. Eliminating an appointment could also lead to significant cost savings, which could make the process less expensive for patients, says Weisenberg. Finding a way to produce dentures more efficiently is critical, he says, since the American College of Prosthodontics estimates that, each year, 15 percent of Americans who wear dentures need to have them replaced. As the Baby Boomer population ages, the demand for dentures is expected to increase.
Now that Weisenberg has filed a provisional patent for his invention, he will spend the next year developing prototypes and conducting additional experiments before starting clinical trials. Though it is still too early to determine whether he will establish a startup company to manufacture the product or license it to an established company, he is excited for the future implications his invention holds. “I find problem solving to be very compelling. I have always been the type to think outside the box,” says Weisenberg. “Innovation doesn’t necessarily mean coming up with a brand new idea. It can mean taking an existing product or process and finding a way to make it better than it was before.”